目录
- 铸造模具制造工厂概述
- 铸造模具制造流程
- 2.1 复磨砂铸造工艺
- 2.2 水玻璃法铸造工艺
- 铸造模具制造工厂的材料选择
- 3.1 钢材
- 3.2 实型铸造材料
- 3.3 铝合金
- 3.4 铸铁
- 铸造模具制造工厂的技术现状与发展趋势
- 4.1 国内外技术对比
- 4.2 技术应用与提升
- 铸造模具常见问题及解决方案
- 5.1 顶针相关问题及解决方案
- 5.2 镶针/镶件问题及解决方案
- 5.3 型腔表面问题及解决方案
- 5.4 浇口套/分流锥问题及解决方案
- 5.5 行位滑块问题及解决方案
- 5.6 油缸密封位及油管接头漏油问题及解决方案
- 铸造模具制造工厂的选择与合作
- 常见问题及回答
1. 铸造模具制造工厂概述
铸造模具制造工厂是专门从事铸造模具设计、生产和加工的工业场所。这些工厂通过一系列复杂的工艺流程,将原材料转化为符合客户需求的模具产品。铸造模具在工业生产中具有广泛的应用,涉及汽车、机械、航空航天、电子等多个领域。随着科技的进步和市场的变化,铸造模具制造工厂也在不断地进行技术创新和设备升级,以满足日益增长的市场需求。
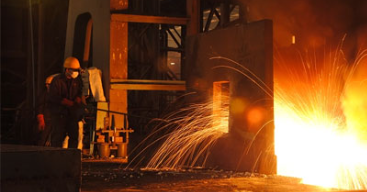
2. 铸造模具制造流程
2.1 复磨砂铸造工艺
复磨砂铸造工艺是铸造模具制造中常用的一种工艺方法。该工艺首先使用硬质合金制作出所需铸件的模具,然后用射砂机将复膜砂射入模具内形成砂型。接下来,将多个砂型组合在一起形成一个完整的铸型。之后,将熔化的金属液从炉子中倒入浇注系统中,通过浇口注入铸型中。等待金属液凝固后,打开铸型,清除附膜砂,取出铸件。最后,使用喷砂机对铸件表面进行喷砂处理,去除氧化皮和毛刺,提高表面质量。
2.2 水玻璃法铸造工艺
水玻璃法铸造工艺是另一种重要的铸造方法。该工艺的主要流程包括制作蜡模、制壳、脱蜡、焙烧和浇注。首先,根据铸件图纸制作蜡模。然后,在蜡模上涂挂耐火材料形成壳型。接着,将壳型中的蜡模熔出,形成型腔。最后,将熔化的金属液倒入型腔中,待金属液凝固后,取出铸件。水玻璃法铸造工艺适用于各种复杂形状的铸件生产,具有铸件尺寸精度高、表面质量好等优点。
3. 铸造模具制造工厂的材料选择
3.1 钢材
钢材在铸造模具制造中具有广泛的应用。以往,钢材主要用于制作砂型铸造模具的标准件和结构件。然而,随着模具加工技术的提升和对铸模尺寸稳定性要求的提高,一些高强度模具钢如H13钢开始用于制作热芯盒和铸模本体。钢材具有高强度、高硬度和良好的耐磨性,能够满足复杂模具的制造需求。
3.2 实型铸造材料
实型铸造是以泡沫塑料板材为材料的一种铸造方法。该方法通过将泡沫塑料板材裁剪并粘贴成所需模样,然后进行浇注而成铸件。实型铸造具有周期短、费用低等优点,适用于小批量和单件生产。随着可加工塑料的应用日益广泛,实型铸造在铸造模具制造中的占比也在逐渐增加。
3.3 铝合金
铝合金因其重量轻、尺寸精度高而受到广泛应用。在铸造模具制造中,铝合金模具常用于制作结构复杂、精度要求高的模具。然而,近年来铝合金模具的应用有所减少,部分市场已被塑料模和铸铁模所取代。尽管如此,铝合金模具在某些特定领域仍具有不可替代的优势。
3.4 铸铁
铸铁是大批量铸造生产的首选材料。铸铁模具具有高强度、高硬度、良好的加工性、成本低和使用寿命长等优点。在铸造模具制造中,铸铁模具常用于制作大型、重型和复杂结构的模具。随着铸造技术的进步,越来越多的模具采用高强度合金灰铸铁或球铁制作,以提高模具的耐磨性和使用寿命。
4. 铸造模具制造工厂的技术现状与发展趋势
4.1 国内外技术对比
发达国家如欧美地区的模具厂多以独立或隶属于大集团的方式运营,规模适中但专业水平高、技术实力强大、生产效率极高。这些企业人员精简,设计、质量控制及营销人员占比超过三成,管理人员控制在5%以内。其年人均产值可观,甚至能达到200万元人民币以上。相较之下,国内模具企业在人员结构上与国外相似,但国企在人员结构上尚需优化。在产值方面,国内企业多数年人均产值在10~20万元人民币之间,少数能达到40万元人民币,与国外企业相比仍有较大差距。
在技术应用方面,国外模具企业普遍采用CAD/CAE/CAM技术,并大量运用逆向工程和快速原型制造等技术。这使得他们的模具价格高昂,制造周期也相对较长。然而,这也从侧面反映了国内模具企业在价格和制造周期上所具备的竞争优势。
4.2 技术应用与提升
近年来,中国压铸工业发展迅猛,年均增长率达到7%~10%。随着高新技术在模具设计和制造中的应用日益广泛,CAD/CAM/CAE技术的普及推动了模具工业的发展,并提升了其国际竞争力。目前,CAD/CAM一体化技术已在铸造模具业中得到了广泛应用。在软件方面,二维设计主要采用AutoCAD,而三维设计则有多种选择,包括Pro/E、UG、Cimatron等。一些领先的铸造模具制造工厂已广泛采用3D设计技术,并运用三维虚拟装配检测技术来确保模具设计的精准度和工艺的合理性。
在模具加工领域,高速加工(HSM)凭借其高切削速度、高进给速度以及高加工质量等特点,受到了越来越多的关注。与普通铣削相比,其加工效率提高了5~10倍,同时还可加工硬材料,如60HRC硬度的工件。因此,在汽车覆盖件模具、压铸模以及大型塑料模具等复杂曲面的加工中,HSM展现出了显著的优势。
此外,随着精密、复杂、大型模具的不断发展,对检测设备的要求也日益提高。目前,精密模具的精度已达到23μm,而铸造模具的精度也要求达到1020μm。快速原型制造铸造模具已进入实用阶段,LOM、SLS等方法的应用可靠性和技术指标已与国外同类产品相当。模具毛坯的快速制造技术也取得了重要进展,包括干砂实型铸造、负压实型铸造以及树脂砂实型铸造等技术。
5. 铸造模具常见问题及解决方案
5.1 顶针相关问题及解决方案
顶针卡死、断顶针是铸造模具常见的问题之一。这可能是由于顶针孔加工时孔径偏小或内表面粗糙、顶针装配过紧等原因造成的。解决方案包括控制顶针孔间隙、加工顶针避空位、注意顶针的维护保养等。此外,顶针印凹入产品面过深或过高也是常见问题,需要通过调整顶针孔尺寸、控制顶针装配精度等措施来解决。
5.2 镶针/镶件问题及解决方案
镶针/镶件断、弯曲、磨损等问题可能是由于材质问题、拔模斜度过小或尺寸过长、碰穿位未留间隙等原因造成的。解决方案包括采用材质好的镶针/镶件、保证拔模斜度和尺寸合理、留足碰穿位间隙等。同时,模具生产时要注意镶针/镶件的维护保养,及时更换损坏的镶针/镶件。
5.3 型腔表面问题及解决方案
型腔表面不光洁、烧模、腐蚀等问题可能是由于模仁材质或热处理问题、操作方法不当等原因造成的。解决方案包括采用材质好的模仁、保证模仁表面热处理后的硬度达到要求、注意模具生产时的维护保养等。此外,模仁加工时要避免顶针、镶针、镶件碰到油路,确保油路封堵良好。
5.4 浇口套/分流锥问题及解决方案
浇口套口部与射咀配合位压伤、水口粘前模、浇口套披锋等问题可能是由于浇口套/分流锥材质或热处理问题、配合间隙过大等原因造成的。解决方案包括采用材质好的浇口套/分流锥、保证配合间隙合理、注意模具生产时的维护保养等。同时,拆装浇口套/分流锥时要轻轻敲出,避免损坏浇口套内孔表面。
5.5 行位滑块问题及解决方案
行位飞料(产品批锋)、滑块卡死、行位碰坏等问题可能是由于前模斜楔强度不够、行位滑块外形尺寸偏小等原因造成的。解决方案包括设计加工时保证前模斜楔和行位滑块的强度足够、保证行位滑块的外形尺寸合理等。同时,模具生产时要注意行位的维护保养,及时清理行位上的异物。
5.6 油缸密封位及油管接头漏油问题及解决方案
油缸密封位漏油、油管接头漏油等问题可能是由于油缸耐高温性能不足、油管接头未接好等原因造成的。解决方案包括使用耐高温的油缸、保证油管接头连接良好等。同时,模具生产时要注意检查油缸和油管接头的状态,及时更换损坏的部件。
6. 铸造模具制造工厂的选择与合作
选择合适的铸造模具制造工厂对于确保产品质量和交货期至关重要。